Resin Sand Molding Line
Foundry / Resin Sand Casting Line
SAND CASTING LINE
NO-BAKE SELF-HARDING RESIN SAND CASTING LINE
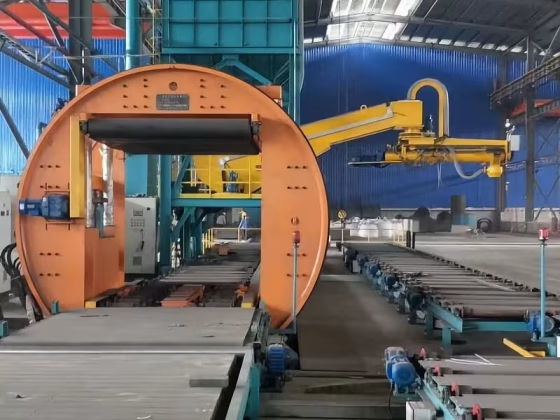
Resin sand casting line, also known as no-bake casting or self-hardening sand-casting technique is involves mixing reclaimed or fresh quartz sand with liquid synthetic furan resin and a catalyst, forming strong molds without heat.
With a typical resin content of 0.7%–1.1% and low free aldehyde levels (<0.3%), this process achieves high mold strength and superior casting quality, ensuring excellent dimensional accuracy, smooth surface finish, and minimal casting defects.
Resin sand casting is suitable for both small and large scale production, meeting international standards across multiple industries. Ideal applicate for producing complex parts in gray iron, ductile iron, carbon steel, and alloy steel, often combined with CNC machining for enhanced precision.
Feature:
1. Precision & Finish
Resin sand casting achieves high dimensional accuracy and smooth surface quality, reducing the need for extensive post-casting machining.
2. Design Flexibility
It produces complex geometries in both small and oversized parts, accommodating diverse metals like iron, steel, aluminum, and copper alloys.
3. Cost Efficiency
Low resin usage (0.8–2.0%), recyclable sand, and minimized waste significantly cut material expenses and production costs, especially for large batches.
4. Process Efficiency
Sand self-hardens at room temperature, requires no drying, and enables easy automation—reducing labor intensity and energy consumption.
5. Environmental Benefit
Generates less waste, allows efficient sand reclamation, and avoids harmful emissions, making it more eco-friendly than traditional casting.
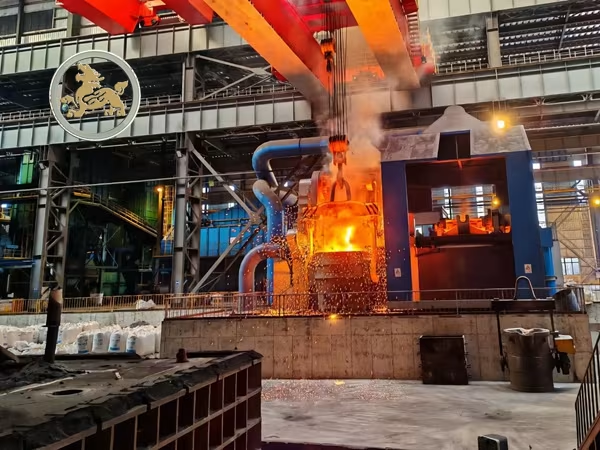
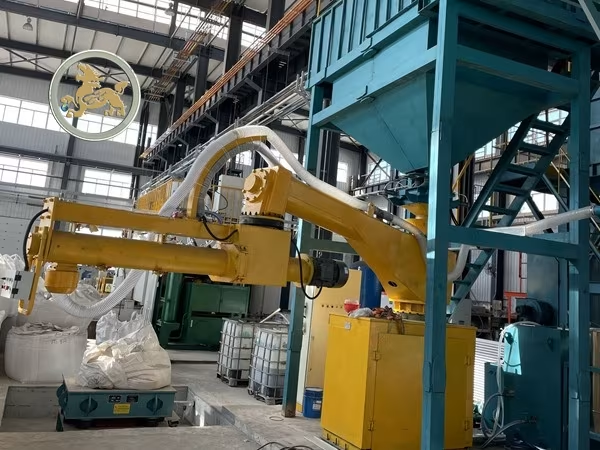
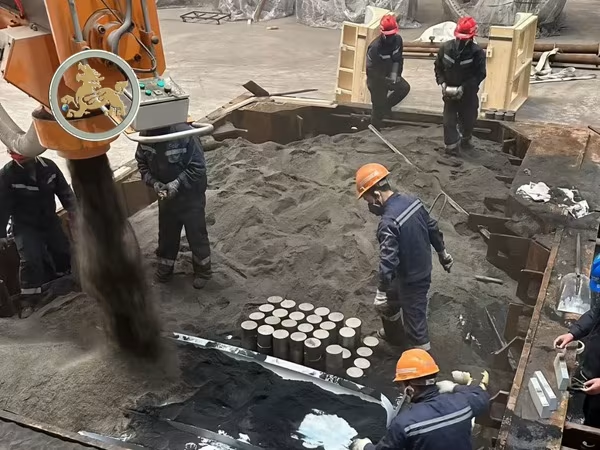
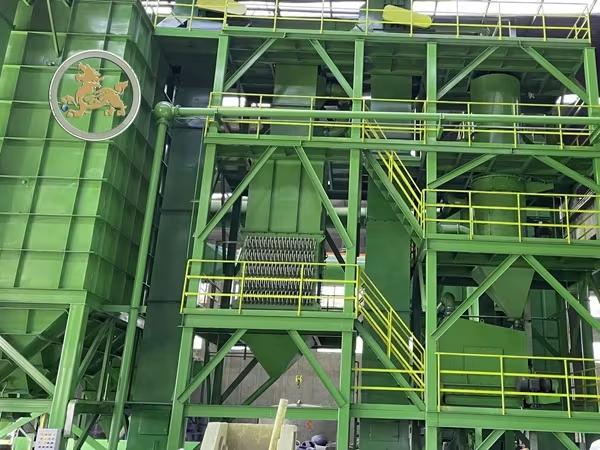
A Step-by-Step Journey for Resin Sand Casting Process:
1. Preparation of Sand Mixing:
Silica sand is combined with a resin binder and catalyst to form a chemically bonded, self-hardening mold mixture.
2. Pattern Preparation:
Patterns, made from wood, plastic, or metal (with aluminum being costlier but superior for high-volume, precision parts), replicate the desired final product.
3. Mold Preparation:
A two-part sand mold that mixed with thermosetting binder (e.g., furan or urethane resin), comprises cope and drag halves.
4. Molding Process:
Resin mixed sand is shoot into cope and drag sand boxes and inside compacted around the pattern to ensure complete fill and solidity, then cures at room temperature before the halves are joined into a complete mold.
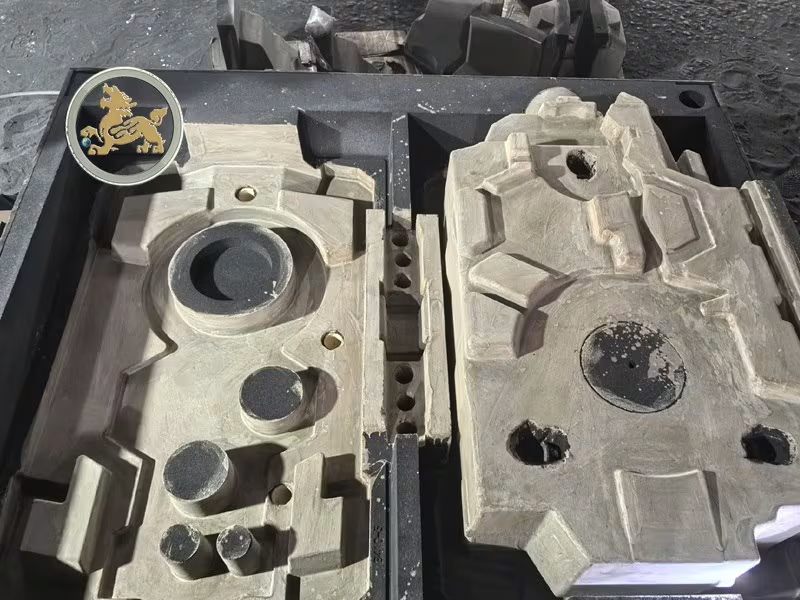
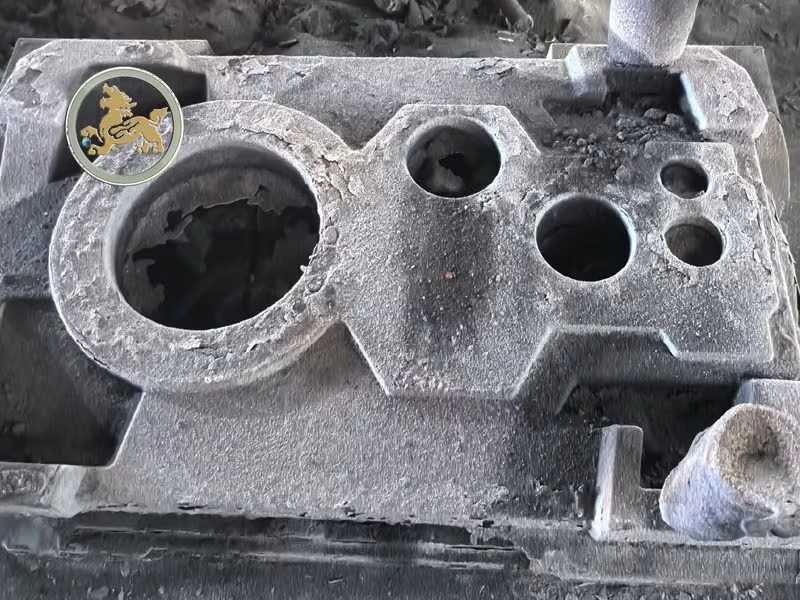
5. Self-Hardening:
Thermally or catalytically cured resin sand is molded around the pattern, coated with an alcohol-based refractory coating, then burned to achieve high solidity to achieve the hard mold casting process.
6. Sand Compaction:
Sand is compacted tightly around the pattern to accurately replicate its shape and ensure structural integrity during metal pouring.
7. Pattern Removal:
After hardened, the pattern is removed, leaving a cavity in the sand mold that replicates the desired metal part’s shape.
8. Metal Pouring:
Molten metal (e.g., aluminum, iron, steel) is poured into the cavity and solidifies, forming the final part.
9. Cooling and Shakeout:
Once the metal cools and solidifies, the sand mold will shakeout and break apart, revealing the casting which is then removed of excess sand.
10. Surface Finishing:
After casting, the part undergoes shot blasting to remove sand and oxides, followed by trimming gates and grinding imperfections; if needed, secondary processes like machining or heat treatment achieve final specifications.
11. Reclamation
Reclaiming used sand and resin reduces waste and costs by recycling them directly into new foundry.
12. Inspection
Final products require defect testing before pricing approval.
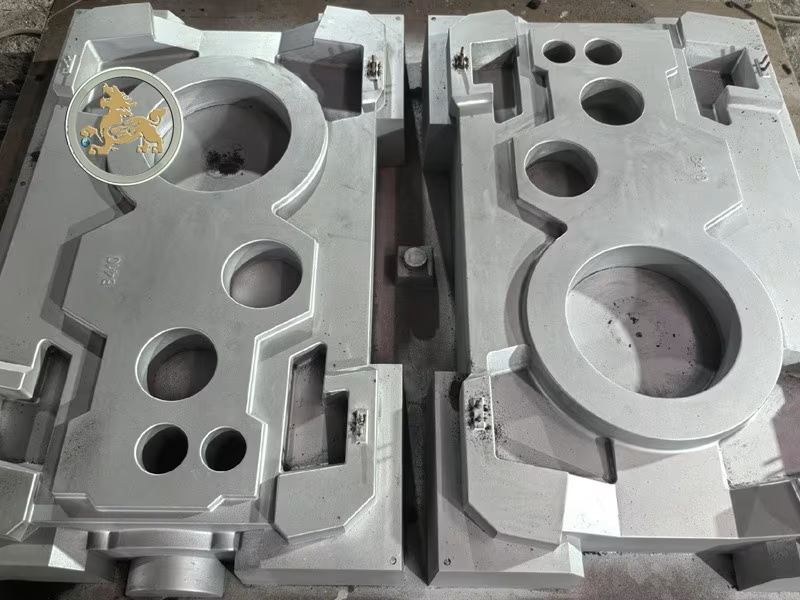