green Sand Molding Line
Foundry / Green Sand Casting Line
SAND CASTING LINE
GREEN SAND CASTING LINE
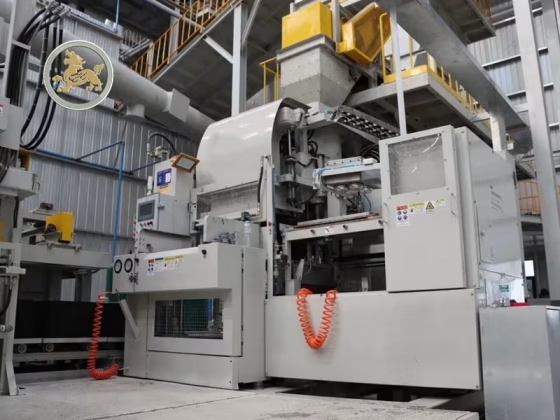
Green sand casting, a traditional and widely used method, involves creating molds from a mixture of sand, clay, water, and additives to cast metal components efficiently and economically. Known for its environmental friendliness and recyclability, green sand casting uses damp, malleable sand—typically a blend of olivine sand, bentonite clay, and water—packed into a mold to form a cavity for molten metal; once the metal solidifies, the sand mold is broken and reused, making this process sustainable and cost-effective.
As one of the oldest and most popular casting techniques, green sand casting produces about 42% of metal castings worldwide, surpassing other methods like no-bake casting. Its versatility suits applications ranging from automotive and electronic parts to cookware and gears, especially for small to medium-sized castings. The term “green” reflects the moist state of the sand, not its color, highlighting the process’s simplicity, repeatability, and long-standing industrial importance.
Feature:
1. Cost-Effective
Green sand casting is economical due to low material costs, minimal equipment investment, and reduced energy consumption, making it budget-friendly.
2. Good Process Performance
This method offers high molding efficiency, achieving good dimensional accuracy and surface quality while allowing gas escape during pouring to minimize defects.
3. Easy Operation
The straightforward nature of green sand casting makes it easy for operators to learn, with flexible production options for manual or machine molding.
4. Environmental-Friendly
Green sand casting is sustainable, as used sand is recyclable, generating minimal waste while providing affordable tooling for versatile, complex shapes.
5. Quick Turnaround & High Capacity
This efficient manufacturing process allows for rapid setup, minimizing lead times and scaling easily for high-volume production with low material costs.
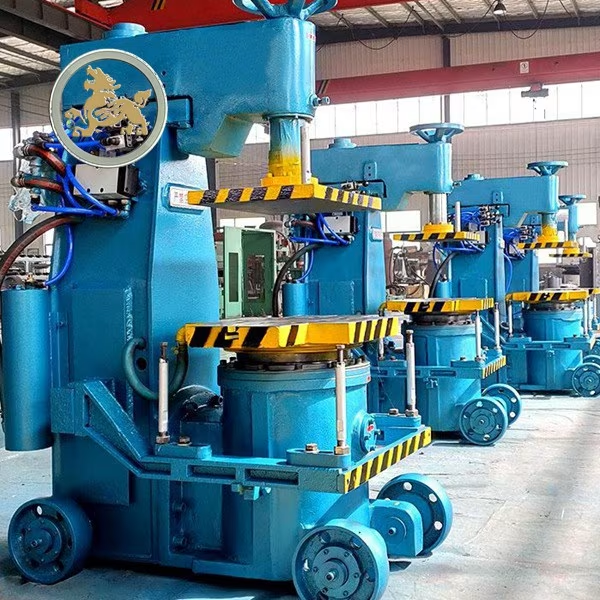
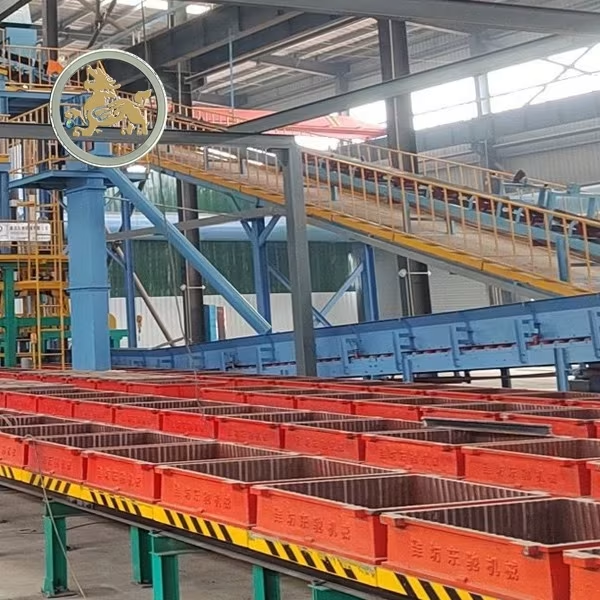
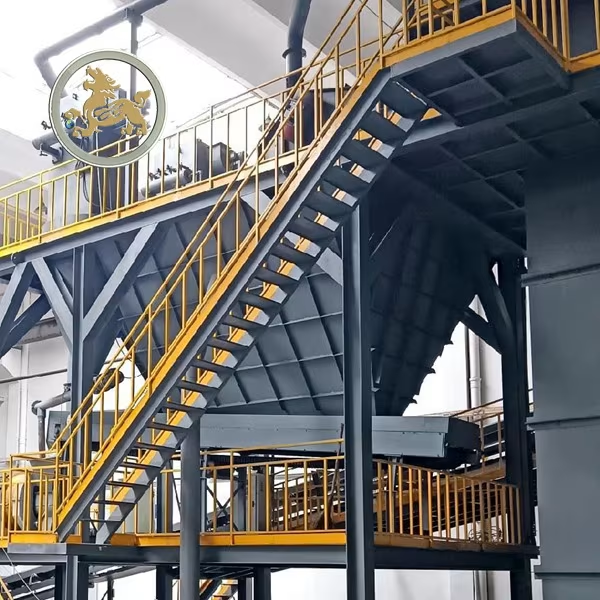
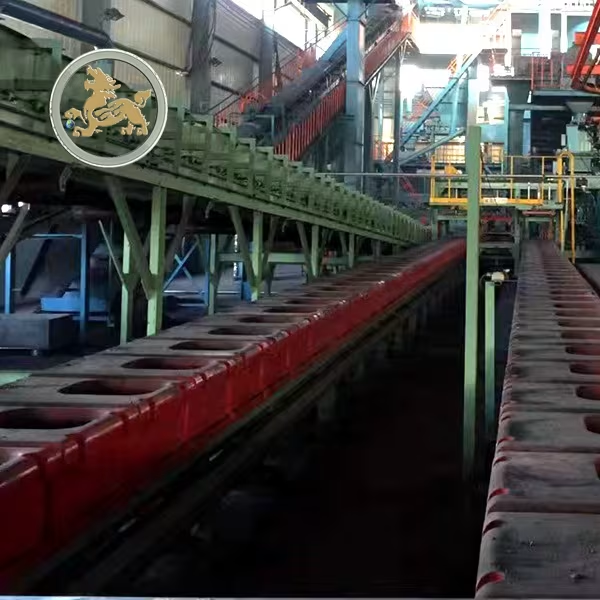
A Step-by-Step Journey for Green Sand Casting Process:
1. Preparation of Green Sand:
Green sand is appliable mixture of silica sand, bentonite clay, water, and additives like coal dust, optimized for effective molding around patterns.
2. Pattern creation
A pattern, made from wood, metal, or plastic, defines the shape of the final metal part and is used to create a sand mold.
3. Molding preparation:
The green sand mixture is packed around a pattern, typically made of wood or metal, to create a mold cavity for the final metal part.
4. Metal Pouring & Cooling:
Similar to resin sand casting, molten metal is poured into the mold cavity, solidifying to take the final shape. After cooling, the mold is disassembled to reveal the cast metal part.
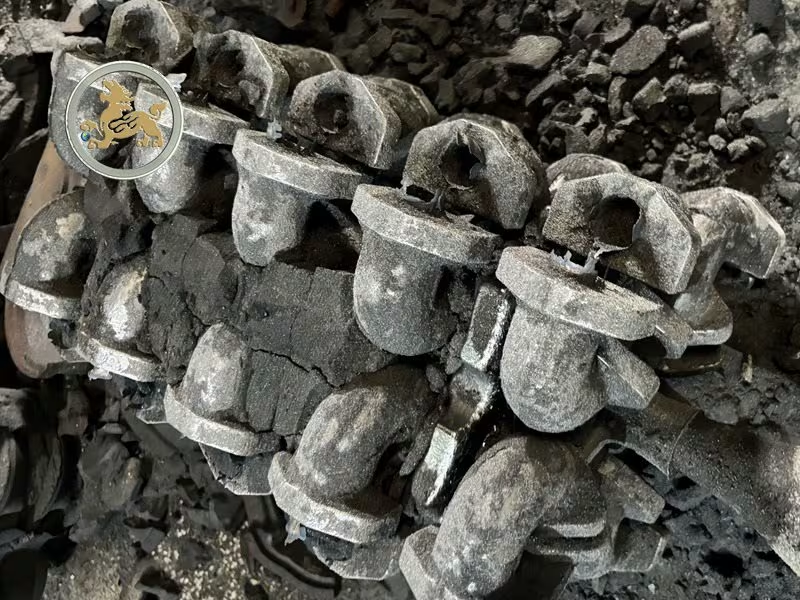
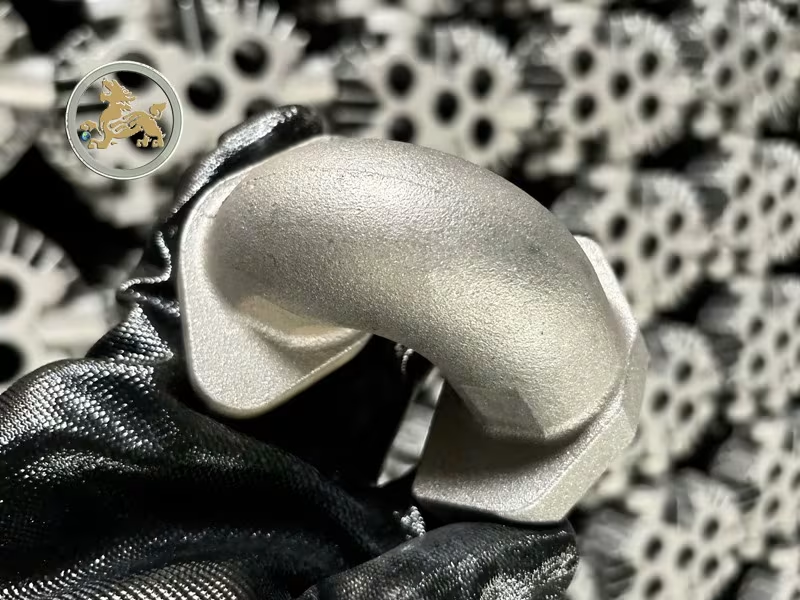
5. Solidification:
After pouring, the metal cools and solidifies in the mold. Cooling rates are controlled using runners, gating, risers, and chills to ensure optimal casting quality.
6. Sand shakeout
After the metal solidifies, the sand mold is broken to release the casting, using mechanical knockout methods like vibratory shakeout machines to remove excess sand.
7. Surface finishing
Residual sand, oxide scale, and burrs are removed through mechanical cleaning methods like shot blasting or grinding, ensuring the casting achieves the desired dimensions and surface finish.
8. Quality Inspection
Final products undergo thorough testing for defects and flaws, including visual inspection, dimensional measurement, and non-destructive testing, before receiving price approval.