Moldeo en arena de resina
Fundición / Fundición en Arena de Resina
FUNDICIÓN EN ARENA
FUNDICIÓN DE MOLDEO EN CÁSCARA ARENA DE RESINA
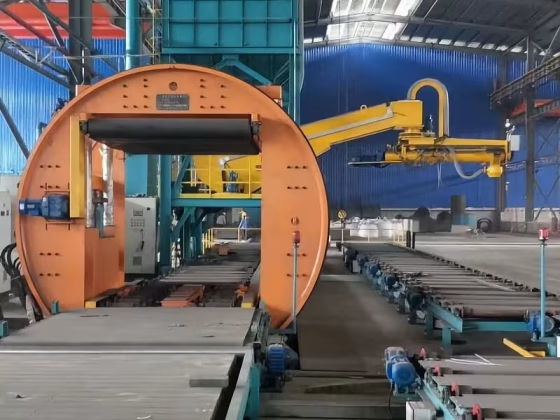
La línea de fundición en arena con resina, también conocida como fundición sin horneado o técnica de fundición en arena autoendurecible, consiste en mezclar arena de cuarzo recuperada o fresca con resina de furano sintética líquida y un catalizador, formando moldes resistentes sin calor.
Con un contenido típico de resina del 0,7%-1,1% y bajos niveles de aldehído libre (<0,3%), este proceso consigue una gran resistencia del molde y una calidad de fundición superior, garantizando una excelente precisión dimensional, un acabado superficial liso y unos defectos de fundición mínimos.
La fundición en arena con resina es adecuada tanto para la producción a pequeña como a gran escala, y cumple las normas internacionales de múltiples industrias. Es ideal para producir piezas complejas de hierro gris, hierro dúctil, acero al carbono y acero aleado, a menudo combinado con mecanizado CNC para una mayor precisión.
Características principales:
1. Precisión y acabado
La moldeo en arena de resina consigue una gran precisión dimensional y una calidad superficial suave, reduciendo la necesidad de un extenso mecanizado posterior a la fundición.
2. Flexibilidad de diseño
Produce geometrías complejas tanto en piezas pequeñas como sobredimensionadas, adaptándose a diversos metales como hierro, acero, aluminio y aleaciones de cobre.
3. Eficiencia de costes
El bajo uso de resina (0,8-2,0%), la arena reciclable y los residuos minimizados reducen significativamente los gastos de material y los costes de producción, especialmente para grandes lotes.
4. Eficiencia del proceso
La arena se autoendurece a temperatura ambiente, no requiere secado y permite una fácil automatización, reduciendo la intensidad de la mano de obra y el consumo de energía.
5. Beneficio medioambiental
Genera menos residuos, permite una recuperación eficaz de la arena y evita emisiones nocivas, por lo que es más respetuosa con el medio ambiente que la fundición tradicional.
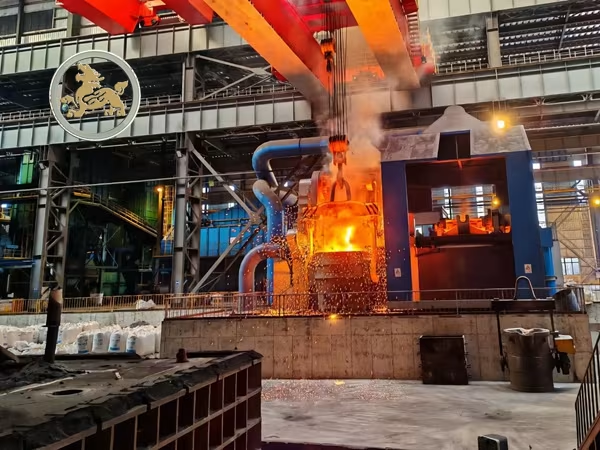
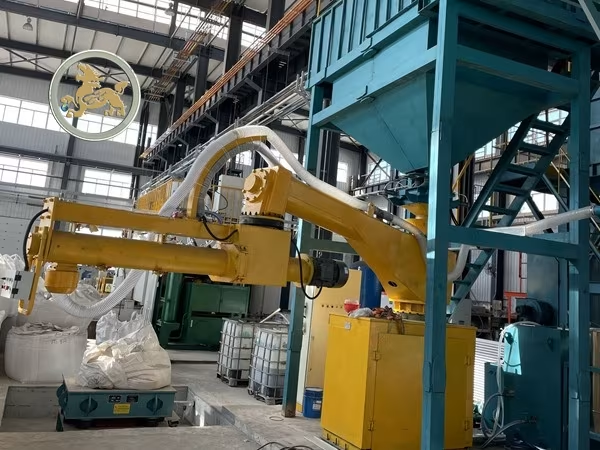
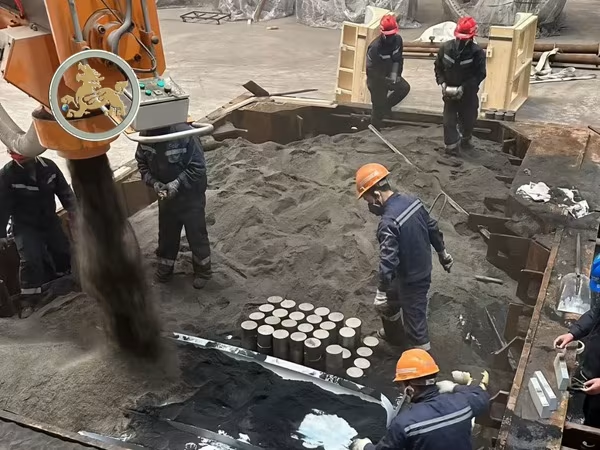
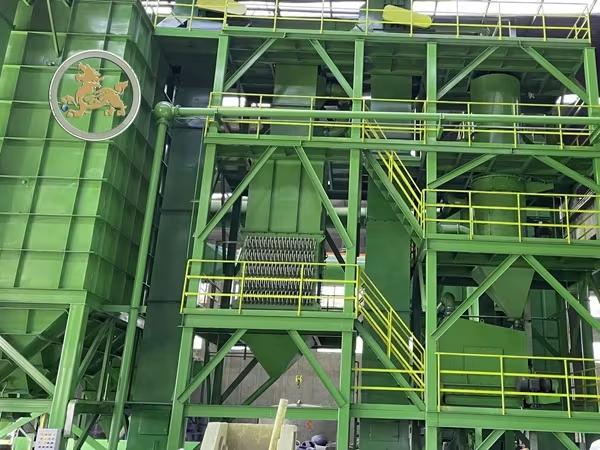
Un viaje paso a paso para el proceso de fundición en arena con resina:
1. Preparación de la mezcla de arena:
La arena de sílice se combina con un aglutinante de resina y un catalizador para formar una mezcla de molde autoendurecible unida químicamente.
2. Preparación del patrón:
Los modelos, fabricados en madera, plástico o metal (el aluminio es más costoso pero superior para piezas de gran volumen y precisión), reproducen el producto final deseado.
3. Preparación del molde:
Un molde de arena de dos partes que mezclado con aglutinante termoendurecible (por ejemplo, resina de furano o uretano), comprende mitades de cope y de arrastre.
4. Proceso de moldeo:
La arena mezclada con resina se dispara en cajas de arena de arrastre y cope y en el interior se compacta alrededor del patrón para garantizar el relleno completo y la solidez, luego se cura a temperatura ambiente antes de que las mitades se unan en un molde completo.
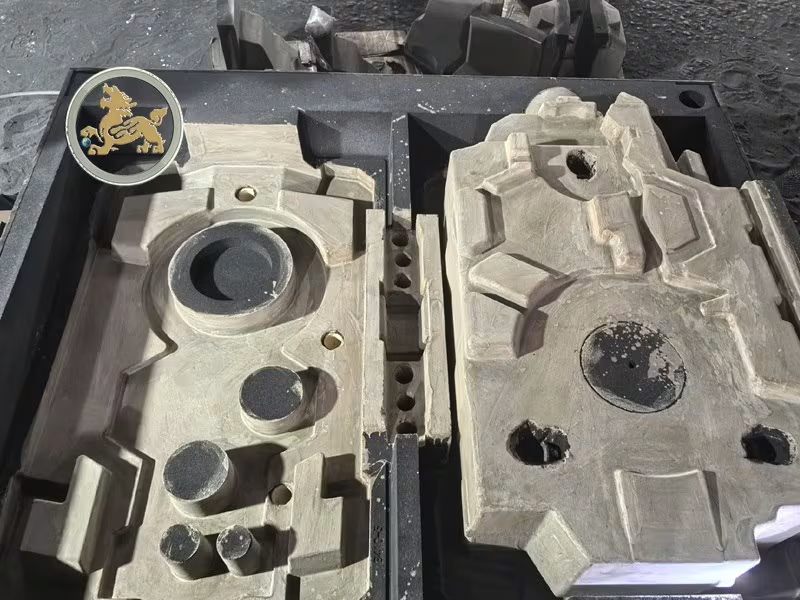
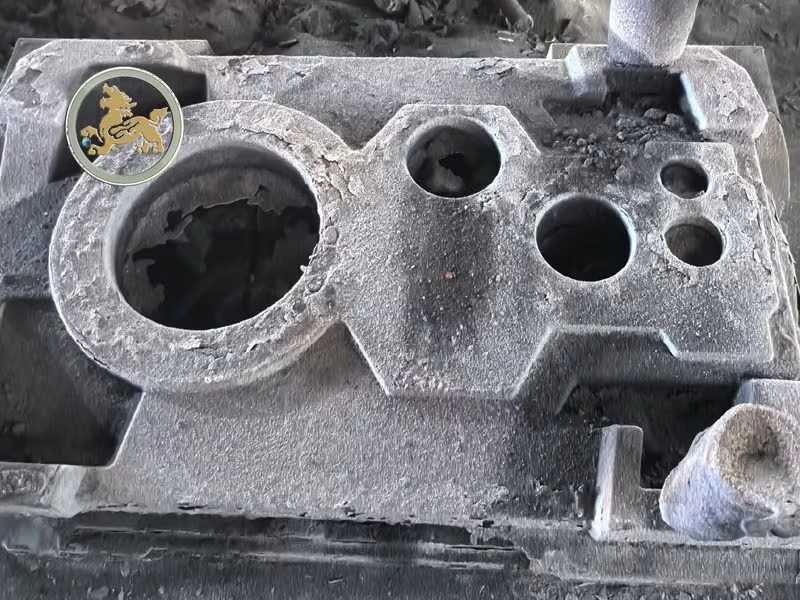
5. Autoendurecible:
La arena de resina curada térmica o catalíticamente se moldea alrededor del patrón, se recubre con un revestimiento refractario a base de alcohol y, a continuación, se quema para conseguir una gran solidez y lograr el proceso de fundición en molde duro.
6. Compactación de la arena:
La arena se compacta firmemente alrededor del patrón para reproducir con precisión su forma y garantizar la integridad estructural durante el vertido del metal.
7. Eliminación del patrón:
Una vez endurecido, el patrón se retira, dejando una cavidad en el molde de arena que reproduce la forma de la pieza metálica deseada.
8. Vertido de metales:
El metal fundido (por ejemplo, aluminio, hierro, acero) se vierte en la cavidad y se solidifica, formando la pieza final.
9. Enfriamiento y Desmoldeo:
Una vez que el metal se enfría y solidifica, el molde de arena se sacude y se rompe, dejando al descubierto la pieza fundida, a la que se retira el exceso de arena.
10. Acabado superficial:
Tras la fundición, la pieza se somete a granallado para eliminar arena y óxidos, seguido de recorte de compuertas y rectificado de imperfecciones; si es necesario, procesos secundarios como el mecanizado o el tratamiento térmico logran las especificaciones finales.
11. Recuperación
La recuperación de arena y resina usadas reduce los residuos y los costes al reciclarlas directamente en una nueva fundición.
12. Inspección
Los productos finales requieren pruebas de defectos antes de la aprobación de precios.
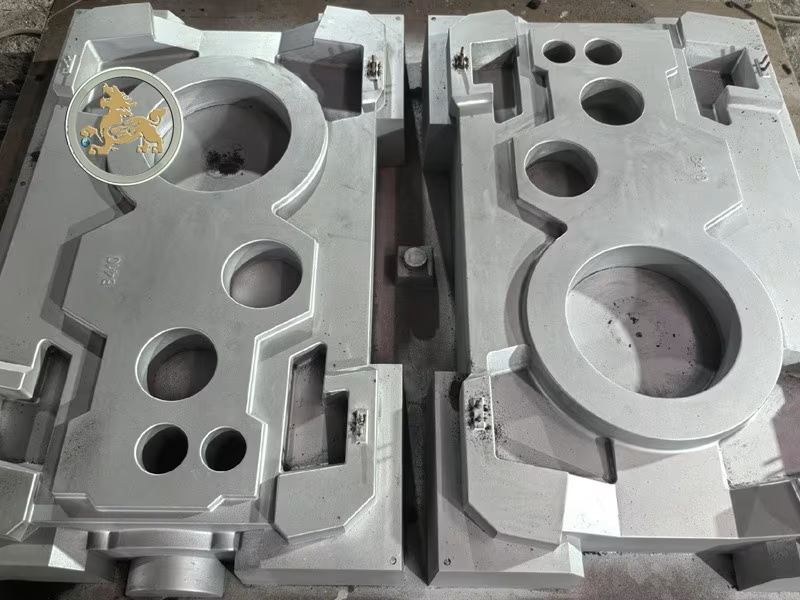